Paper-based printing has many applications beyond traditional document printing. One application is in microfluidic devices, specifically microfluidic paper-based analytical devices (µPADs). These devices use the channels in paper to control and manipulate fluids for chemical and biological analyses. They are used for point-of-care diagnostics, allowing for quick and cost-effective testing in resource-limited settings. Another application is in filters. Filter papers, made from special fibers, separate and purify substances in laboratories and testing environments. The paper’s porosity and structure make it ideal for filtration and separation. Paper-based printing is also used for rapid prototyping. It is low-cost and easily shaped, making it valuable for creating small-scale models in product development. Overall, paper-based printing has versatile applications in various industries, showing its continued relevance in the digital age.
Care Diagnostics
Care Diagnostics is a field that utilizes paper-based printing to create fully integrated electrochemical biosensors, revolutionizing the way medical diagnostic tests are performed. These biosensors hold the potential to transfer measured data directly to a user’s smartphone, making healthcare more accessible and convenient.
The process begins by designing the biosensor on a computer, specifying the desired detection method and biochemical reactions involved. Inkjet printing is then used to dispense the bioactive reagents onto designated areas of the paper-based sensor, creating the necessary specific recognition sites.
The printed biosensor is integrated with electrochemical detection components to precisely measure the concentration of analytes in a test sample. The result is then transmitted wirelessly to a user’s smartphone for analysis and interpretation, enabling real-time monitoring of health conditions and quick decision-making regarding further medical interventions.
By utilizing paper-based printing and inkjet technology, care diagnostics is advancing towards creating portable and user-friendly biosensors that can be easily deployed in remote areas or underserved communities. These breakthroughs in fabrication technologies are paving the way for more affordable and accessible healthcare solutions for all.
Filter Papers and Sheets for Testing and Laboratories
Filter papers and sheets are essential tools in the field of laboratory testing and filtration. They are specifically designed to separate solid particles from liquids or gases, ensuring a clean and accurate analysis.
Filter papers come in various types and grades, each with its specific characteristics and applications. For instance, qualitative filter papers are used for general filtration purposes, while quantitative filter papers are designed for precise quantitative analysis. Ashless filter papers are commonly utilized in testing for heavy metals and other contaminants that could affect the accuracy of the results.
In addition to filter papers, filter sheets are also widely used in laboratory environments. These sheets are typically made from cellulose fibers and are ideal for large-scale filtration processes. They are efficient at removing particles and impurities from liquids, making them indispensable in industries such as food and beverage, pharmaceuticals, and environmental testing.
Filter papers and sheets play a crucial role in a variety of applications. They are used in laboratory testing to separate solids from liquids or gases, ensuring the purity of the tested samples. They are also employed in industrial processes to filter out impurities, ensuring the quality and reliability of the final products. Furthermore, filter papers and sheets are utilized in environmental testing to analyze pollutants and contaminants in air and water samples.
Rapid Prototyping and Institutional Affiliations
Rapid prototyping is a valuable tool in the product development process, allowing for the creation of prototypes and models quickly and cost-effectively. Paper-based printing is an increasingly popular method for rapid prototyping, offering numerous advantages over traditional methods.
Institutional affiliations play a crucial role in the adoption and utilization of paper-based printing for rapid prototyping. Many universities, research institutions, and corporate laboratories have embraced this technology, recognizing its potential for innovation and efficiency. These affiliations provide a supportive environment for research and development, as well as access to state-of-the-art equipment and resources.
Paper-based printing allows for the creation of prototypes and models using various paper substrates, printing techniques, and design software. It offers flexibility in terms of shape, size, and complexity, making it suitable for a wide range of applications. With the ability to rapidly iterate designs and incorporate feedback, paper-based printing accelerates the product development cycle.
Jurisdictional Claims and Methods for Paper Manufacturing
Jurisdictional claims and methods for paper manufacturing are crucial aspects of the paper-based printing industry. Jurisdictional claims refer to the legal rights and control that countries or regions have over the manufacturing and distribution of paper products. These claims determine the regulations, standards, and practices that govern the industry.
The methods for paper manufacturing involve several processes, including printing and coating. Printing is the technique used to transfer ink onto the paper surface, creating text, images, or patterns. It can be done using various methods such as offset printing, digital printing, or inkjet printing. Coating, on the other hand, involves applying a layer of material onto the paper surface to enhance its durability, appearance, or functionality. This can include coatings for gloss, matte, or special finishes.
In the paper-based printing industry, it is vital to adhere to copyright laws and acknowledge institutional affiliations. Copyright laws protect intellectual property and prevent unauthorized use of copyrighted material. Paper manufacturers and designers need to respect these laws and obtain proper permissions or licenses when using copyrighted content.
Acknowledging institutional affiliations is also crucial in the paper-based printing industry. Institutions such as universities, research organizations, and corporate laboratories play a significant role in driving innovation and development in this field. By acknowledging these affiliations, manufacturers, and designers can establish credibility and strengthen their relationships with these institutions.
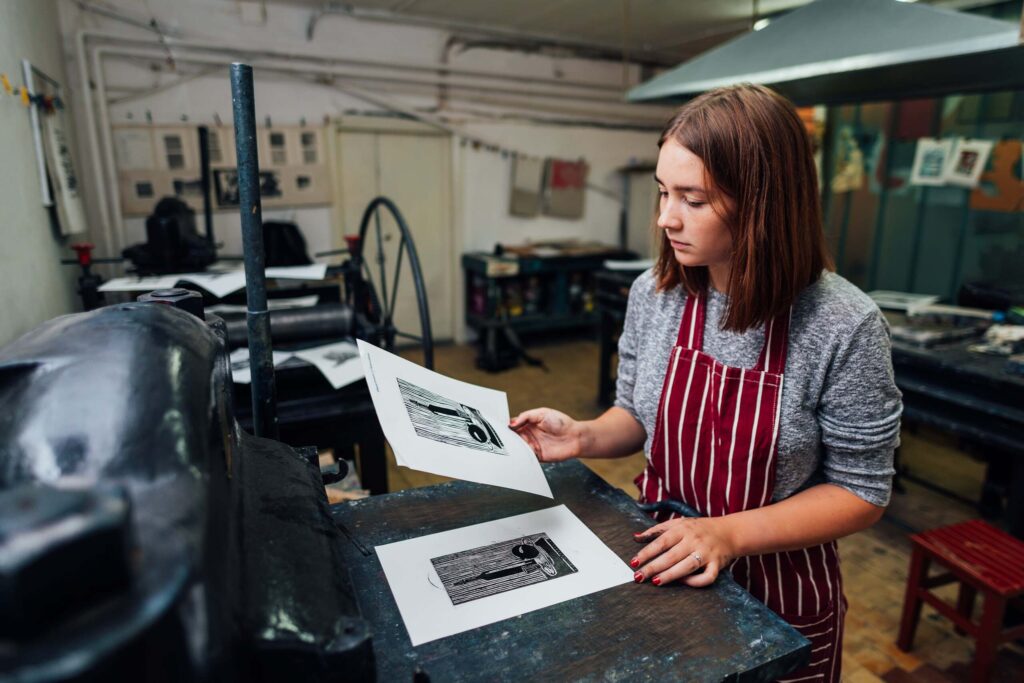
Conclusion
In summary, paper-based printing has found applications in diverse fields, including care diagnostics, filter papers, rapid prototyping, and institutional affiliations. The continuous advancement of this technology has the potential to further impact multiple industries and improve accessibility to essential diagnostic tools and devices.